Why can’t I fix my own phone, toaster, or camera?
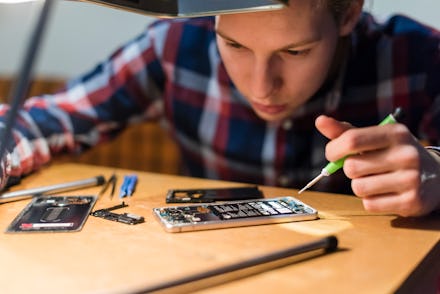
This article was originally published by The Markup, a nonprofit newsroom covering the ways technology is changing society. Follow them on Twitter and Facebook, and subscribe to their newsletter here.
As critically ill COVID-19 patients started showing up in droves at emergency rooms around the world, ventilators became a crucial technology keeping patients alive. When hospitals’ own resources became overwhelmed, the Strategic National Stockpile dusted off and distributed thousands of the life-support machines throughout the country.
But not all were in working condition.
J. Scot Mackeil, a biomedical technician with more than 40 years of experience, worked on a team tasked with inspecting machines sent to Massachusetts’s Emergency Management Agency. In mid-April, while performing spot checks on hundreds of ventilators packed in freight pods, Mackeil discovered one with a damaged power connector.
But when he asked the manufacturer to send him a replacement part, he was surprised to receive the manufacturer’s response: “ ‘Absolutely no.’ ”
“I had just expected, ‘Oh, no problem. Where can we send it?’ ” he said. “I wasn’t expecting them to dig their heels in.”
Mackeil was well aware of what’s become a common obstacle for hospitals: Manufacturers not only have a monopoly over even simple replacement parts, but they also often allow only their authorized service technicians to repair equipment.
Mackeil told The Markup that over his career, manufacturers resisting hospitals doing their own repairs has become the norm.
“Medical equipment manufacturers look at the service phase of the device life as a huge profit center,” Mackeil said.
With the ventilator, he had thought they might relent.
“It was just a shame,” he said.
It’s not just medical device manufacturers who keep a tight grip on the inner workings of the products they sell—mobile phones, game consoles, coffee makers, and farm equipment all share examples of the same sort of repair restrictions that advocates calling for “right to repair” laws seek to eliminate.
And though you might technically own your camera, game console, blender, or phone, you repair it at your own peril. Going outside the official route for fixes is either impractical without repair manuals and proprietary tools or could void the machine’s warranty (though consumers have some protections on that front).
“We are no longer able to fix the things we buy,” said Gay Gordon-Byrne, who is the executive director of The Repair Association, a coalition of businesses and organizations seeking legislation across the country that would give consumers the right to repair their own machines.
The right-to-repair movement has drawn an unusual coalition of stakeholders, including environmentalists, libertarians, engineers, independent repair shop owners, gamers, hobbyists, and farmers.
Groups like The Repair Association have helped push consumer electronic right-to-repair bills introduced in dozens of states. None, however, have become law in recent years.
Lobbyists for the electronics manufacturers have also raised concerns that unqualified repairs could lead to dangerous failures of their products and that states with right-to-repair laws could become havens for hackers.
Such laws could eliminate a manufacturer’s monopoly on not only who can fix a product — but also on when a product is essentially deemed unfixable.
Why Won’t Apple Fix My Phone? Can Someone Else Do It?
Today’s mobile phone is a marvel of precision engineering — watertight seams, sealed batteries, and a lack of visible fasteners that would make most consumers unsure of how you would even go about opening it. To get inside requires detailed schematics, diagrams, and specialized tools.
Apple has all of those, of course, but in July 2019, Apple VP Kyle Andeer testified to Congress that the company and its authorized service providers perform only four types of iPhone repair: display, battery, speaker, and camera. If your phone dies (when it is no longer covered by warranty or optional AppleCare coverage) and it can’t be fixed by one of those repairs, Apple may suggest you buy another phone.
Jessa Jones, founder of iPad Rehab, a mobile device repair shop in Honeoye Falls, N.Y., says that’s disingenuous.
“I think that my customers are largely unaware that what they’re being told by the manufacturer of the device, about the problem that they’re having and about the repairability of that problem, is false,” she told The Markup.
“We aim to avoid the need for repair in the first place,” Apple spokesperson Keri Fulton said in a statement to The Markup. “But when a repair is needed, there should be safe, dependable options available to bring a device back to its best possible performance.”
Jones runs a popular YouTube channel on which she uses her soldering skills under a microscope to perform several repairs that Apple does not offer.
She particularly specializes in restoring data from dead phones—often helping people recover precious photos of loved ones.
“There’s a chip on the board that is soldered on there that contains all of your memories, and those memories are encrypted by default,” Jones said, and it’s time-consuming though entirely possible to retrieve.
Our ability to just take something from the junkyard of iPhone parts and plug it into your new phone is becoming increasingly limited. - Jessa Jones, founder of iPad Rehab
“The only way to decrypt that and get them back out is you’ve got to get a multi-meter out and solve problems on that logic board,” she said.
Jones also noted that there are many relatively simple repairs that shouldn’t require a trip to the Apple Store or an authorized dealer.
Tips are easy to find online, and sites like iFixit offer detailed repair guides, tools, and replacement parts. Independent phone repair shops can be found in towns large and small, but they often operate without official manufacturer certifications to repair devices. These shops may use unofficial aftermarket parts from overseas, or replacement parts harvested from inoperable phones.
But like many other device manufacturers, Apple increasingly employs strict digital controls over the hardware that the device detects, making non-Apple repairs of some components impossible without Apple diagnostic tools.
“Our ability to just take something from the junkyard of iPhone parts and plug it into your new phone is becoming increasingly limited, because the parts are now serialized, meaning there’s a serial number in the part that the phone refuses to operate [without],” said Jones.
Fulton from Apple declined to comment but pointed The Markup to the company’s 2020 Environment Report, which says products are becoming easier to repair.
“For our iPhone devices, we’ve utilized stretch release adhesives, which securely hold the battery during use yet can be swiftly debonded by service partners to install replacements,” the report says.
Apple is not alone in making devices that are hard to repair. Jones said manufacturers of Android devices employ manufacturing techniques that make repairs difficult. iFixit CEO Kyle Wiens told The Markup, though, that there are manufacturers who are voluntarily adopting right-to-repair principles.
“Motorola is the first smartphone manufacturer that stepped up and is basically complying with right to repair,” he said. “They have worked with us.”
There’s a Diverse, Growing Movement Behind the Right to Repair — but It Faces Hurdles
Some of the earliest calls for right-to-repair legislation came from farmers, who’ve been struggling for the ability to fix their own John Deere tractors for years. John Deere equipment is sold with software restrictions that only authorized technicians can bypass, frustrating traditionally self-reliant farmers.
During their campaigns for president, both Elizabeth Warren and Bernie Sanders cited the plight of these farmers unable to repair their own equipment and called for a national right-to-repair law as part of a host of proposals to help American farmers that ended up being adopted as a plank in the Democratic platform for 2020.
A spokesperson for John Deere declined to comment.
The company has recently made an effort to smooth things over, offering a program with diagnostics, training, and documentation for farmers wanting to do their own repairs, starting in 2021.
In 2018, an alliance of right-to-repair advocates won long-sought exemptions to the Digital Millennium Copyright Act to allow farmers and other consumers to break software locks on the products they own — without breaking the law. These latest exemptions (which are considered every three years under the law) enable the legal “jailbreaking” of new phones, voice assistants, and software locks on tractors, cars, and home appliances — though not on video game consoles. Importantly, they also allow you to hire someone to do this breaking for you.
Massachusetts, where a voter-initiative automotive right-to-repair law passed in 2012 with 86 percent voting in favor, shows the potential popularity of expanding such laws.
This November, Massachusetts voters will consider an update to the automotive law, which would allow consumers to access and control the automobile diagnostic and telemetric data that’s increasingly sent directly to car manufacturers via cellular radios.
Massachusetts also has a consumer electronics right-to-repair bill that advocates say is the furthest along of any in the country, though it’s currently awaiting a vote by both chambers of the state legislature.
The Massachusetts bill has served as a template for proposed automotive and consumer electronic right-to-repair legislation around the country—some of which has come close to becoming law, only to be killed at the last minute by lobbying from electronics and automobile manufacturers. New York State lobbying disclosures for 2018, for instance, show that Apple, Verizon, Facebook, AT&T, Toyota, Caterpillar, and others all successfully lobbied against a proposed “Fair Repair Act.”
Industry groups opposing right to repair include Consumer Technology Association, Association of Equipment Manufacturers, and TechNet (a large industry group whose members include Apple, Amazon, Google, Facebook, and Comcast).
In 2019, TechNet’s then Northeast executive director, Christina Fisher, testified before the Massachusetts state legislature’s Joint Committee on Consumer Protection and Professional Licensure in opposition to the proposed digital right-to-repair bill.
Fisher argued that the bill was “legislation in search of a problem”—that consumers already have plenty of choices for repairs and that such laws would hurt innovation.
TechNet declined to comment for this story, pointing The Markup to the group’s previous statements.
An all-star list of engineers and cyber security professionals founded Securepairs in 2018 to counter these arguments, which the group says are without merit.
What Comes Next?
If Massachusetts were to pass the nation’s first consumer electronic right-to-repair law, it could have national influence. When the Massachusetts Automotive Right to Repair bill passed in 2012, all major car manufacturers signed a memorandum of understanding voluntarily adopting the requirements of the Massachusetts law nationwide.
Aside from legislation, Apple does appear to be moving forward with several efforts at increasing the availability of parts and repairs for its products, but recent internal emails, disclosed as part of a U.S. House antitrust subcommittee hearing in July, show internal confusion surrounding these initiatives.
“What is our repair strategy? Are we comfortable releasing our repair manuals for all products moving forward?” read one email from Lori Lodes, Apple’s former director of corporate communications, from March 2019.
Apple declined to comment on these emails directly and referred The Markup back to its 2020 Environment Report, in which the company says it has “broadened the reach of Apple authorized service repair. Through a partnership with Best Buy, we added 1000 more AASP locations in 2019, tripling the number of U.S. AASP locations compared to three years ago.”
Meanwhile, prompted by the pandemic, there’s a bit of a guerrilla movement afoot, at least when it comes to medical devices.
When Wiens, CEO of repair website iFixit, heard about the crisis of the shortage of ventilators in Italy as that country struggled at the height of its first wave of COVID-19 cases, he wanted to help. Aside from selling replacement parts and repair tools, iFixit offers detailed documentation for repairing electronics—and Wiens decided they could do something similar for crucial medical equipment.
Wiens and his team collaborated with volunteers to collect and organize a free library of more than 13,000 service and maintenance manuals for lifesaving medical equipment. The move was potentially legally risky, but so far, the materials remain online.